Feb 25, 2025
The Importance of Quality Management Systems in Aerospace & Defense
What is a Quality Management System (QMS)?
A Quality Management System (QMS) is a structured framework that defines an organization’s
quality policies, objectives, and processes to ensure products meet regulatory, safety, and
performance standards. In aerospace and defense (A&D) manufacturing, where precision and
reliability are non-negotiable, a well-implemented QMS provides the foundation for operational
excellence and compliance with stringent industry regulations.
A QMS encompasses several core functions, including document control, process
standardization, risk management, and continuous improvement initiatives. By maintaining
consistent quality throughout the production cycle, manufacturers can mitigate risks by
enhancing efficiency, thereby ensuring customer satisfaction.
The Critical Role of QMS in Aerospace & Defense Manufacturing
Quality control in A&D manufacturing is crucial due to the high stakes involved in product
safety, operational reliability, and compliance with industry regulations. Even minor defects can
lead to catastrophic failures, making robust quality assurance and quality control an imperative.
● Ensuring Product Integrity: Components in aircraft, defense systems, and space
technology must withstand extreme conditions. Quality control measures such as
inspections, material testing, and performance evaluations prevent defects that could
compromise safety.
● Regulatory Compliance: Industry standards such as AS9100 and ISO 9001 govern A&D
manufacturing. These certifications ensure that manufacturers adhere to best practices
and are recognized by regulatory bodies like the Federal Aviation Administration (FAA)
and the Department of Defense (DoD).
● Supplier and Production Oversight: Many A&D manufacturers rely on a complex supply
chain. A robust QMS ensures supplier quality, traceability of materials, and adherence to
compliance requirements.
Effective quality control also minimizes costly recalls, production downtime, and reputational
damage, reinforcing the importance of a QMS in delivering mission-critical products.
TIPQA: The Premier QMS Software for A&D
To meet the rigorous demands of A&D manufacturing, organizations need a QMS that integrates
seamlessly with enterprise systems while providing comprehensive quality oversight. TIPQA by
Deltek TIP Technologies stands out as a best-in-class solution, offering a digitized approach to
quality management that enhances accuracy, compliance, and operational efficiency.
Key Capabilities of TIPQA
● End-to-End Quality Oversight: TIPQA streamlines quality management across the entire
product lifecycle, from supplier validation to final product inspection.
● Integrated Compliance Management: With built-in compliance tracking for AS9100, ISO
9001, and FAA regulations, TIPQA helps organizations stay audit-ready and compliant.
● Nonconformance and CAPA Management: The system provides robust tools for tracking
nonconformances, implementing corrective and preventive actions (CAPA), and
mitigating risks before they escalate.
● Advanced Audit Capabilities: TIPQA facilitates internal and external audits with detailed
documentation and traceability, ensuring manufacturers meet regulatory and contractual
requirements.
● Supplier Quality Management: The software enables manufacturers to monitor supplier
performance, conduct audits, and enforce compliance with industry standards.
Competitive Advantages of TIPQA
TIPQA is not just a quality management tool—it is a strategic asset for A&D manufacturers.
Unlike generic QMS solutions, TIPQA is specifically designed for the complex regulatory and
production environments of aerospace and defense. Its Safety Element Approval from the FAA
underscores its credibility and commitment to high-quality standards.
By leveraging TIPQA, manufacturers can:
● Improve first-pass yield rates and reduce scrap and rework.
● Enhance collaboration between engineering, production, and quality teams.
● Maintain comprehensive documentation and traceability for audits and compliance.
Integrating QMS with ERP and Enterprise Systems
A modern QMS cannot operate in isolation; it must integrate with Enterprise Resource Planning
(ERP) and other enterprise systems to provide a holistic view of quality and manufacturing data.
This integration enhances visibility, reduces manual data entry, and ensures quality remains a
core focus throughout the production process.
TIPQA and Deltek Costpoint: A Unified Solution
For A&D manufacturers using Deltek Costpoint, TIPQA offers seamless integration to create a
unified environment for quality and manufacturing management. Key benefits of this integration
include:
● Real-Time Quality Data Synchronization: TIPQA and Costpoint work together to provide
real-time visibility into quality metrics, enabling proactive decision-making.
● Paperless Shop Floor Execution: With TIP Shop Floor Execution, quality and production
data are digitally linked, eliminating inefficiencies associated with paper-based processes.
● Closed-Loop Quality Control: Quality issues detected on the shop floor can trigger
immediate corrective actions within TIPQA, ensuring continuous improvement.
● Open API Integration: TIPQA supports multiple ERP interfaces, including SAP and
Oracle, allowing manufacturers to integrate quality management with their existing
enterprise solutions.
Enhancing Operational Efficiency Through Integration
Integrating QMS with ERP unlocks several operational benefits:
● Automated Compliance Tracking: Ensures adherence to industry standards without
manual intervention.
● Improved Resource Planning: Aligns quality data with inventory and production
schedules, optimizing workflows.
● Data-Driven Decision Making: Provides executives and managers with actionable
insights to drive efficiency and quality improvements.
By aligning QMS with ERP, A&D manufacturers gain a true enterprise-wide picture of quality,
ensuring that quality management is not just a compliance requirement but a strategic advantage
in a competitive industry.
Conclusion
A robust Quality Management System is essential for Aerospace & Defense manufacturers to
ensure product reliability, regulatory compliance, and operational excellence. TIPQA by Deltek
TIP Technologies stands out as the premier QMS solution, offering comprehensive quality
oversight, seamless ERP integration, and industry-specific features that help manufacturers
maintain the highest quality standards while improving efficiency.
By leveraging TIPQA and integrating it with Deltek Costpoint, manufacturers can optimize their
quality processes, reduce risks, and drive continuous improvement—ensuring long-term success
in the highly regulated and competitive A&D sector.
Nov 5, 2024
NEW BLOG POST: COMPLIANCE / FINANCE
Finance teams are increasingly turning to technology to enhance financial performance. Despite some financial metrics, such as growth rates and P/L margins, softening this year compared to 2022’s historic highs, the results still outperform most years recorded by the Clarity survey. As finance professionals focus on managing costs and profitability, they also face talent pressures that impact the government contracting industry. Fortunately, technology serves as a force multiplier, with tools like AI helping reduce costs and allowing personnel to concentrate on more strategic tasks.
In the government contracting industry, technology such as Enterprise Resource Planning (ERP) systems can significantly mitigate and facilitate compliance issues. ERP systems streamline processes and provide comprehensive oversight, ensuring that financial and operational activities align with regulatory requirements. These systems offer integrated solutions for tracking expenses, managing contracts, and maintaining detailed records, which are essential for compliance with government contracts. By automating compliance-related tasks, ERP systems reduce the risk of human error, improve accuracy, and ensure that companies can quickly adapt to new regulations.
High performers in the financial sector are not only focusing on talent acquisition and retention but also utilizing technology to manage audits and compliance efficiently. The systematic approach to audits, supported by dedicated resources, reflects a broader trend of leveraging technology to optimize financial and operational functions. This strategy allows companies to remain agile and competitive, even as they face challenges related to talent and compliance in the complex landscape of government contracting.
Overall, high-performing financial teams in the government contracting industry demonstrate how technology, particularly ERP systems, can address compliance issues effectively while also optimizing other critical business functions. By staying ahead of the curve and embracing digital transformation, these teams set a benchmark for operational excellence and regulatory adherence.
Why Deltek Costpoint™ is the BEST ERP for compliance and DoD requirements
Compliance with Government Regulations: Costpoint™ is specifically designed to help government contractors meet stringent regulatory requirements. It ensures compliance with standards such as FAR (Federal Acquisition Regulation), DFARS (Defense Federal Acquisition Regulation Supplement), and CAS (Cost Accounting Standards), making it easier for contractors to adhere to government mandates.
Project Management: Costpoint™ offers comprehensive project management capabilities that are essential for government contractors. It integrates project planning, budgeting, scheduling, and resource management, ensuring that projects are delivered on time and within budget while meeting all contractual requirements.
Accurate Cost Accounting: Costpoint™ provides robust cost accounting features that allow government contractors to track and manage costs accurately. Its detailed cost reporting and allocation capabilities ensure precise cost control, which is critical for government contracts that require meticulous cost tracking and auditing.
Enhanced Security and Data Protection: Government contractors handle sensitive information, and Costpoint™ addresses this need with advanced security features. It offers strong data protection measures, including encryption, access controls, and compliance with cybersecurity standards such as NIST (National Institute of Standards and Technology).
Scalability and Flexibility: Costpoint™ is highly scalable and can accommodate the growth and evolving needs of government contractors. Its flexible architecture allows for customization to meet specific contract requirements, making it suitable for contractors of all sizes, from small businesses to large enterprises.
Oct 3, 2024
MANUFACTURING/SUPPLY CHAIN
The manufacturing sector is experiencing significant technological advancements, with automation and artificial intelligence (AI) being key tools to address workforce turnover while maintaining quality standards. One of the industry’s primary concerns remains the supply chain, but an even greater challenge is replacing experienced workers who are aging out of the workforce. Although manufacturers have identified technological initiatives and other strategies to manage these issues, the follow-through to invest in and scale these systems remains a significant obstacle. In 2024, talent acquisition and quality control remain the top challenges, with talent attraction and retention being the most critical issue for this year, cited by 33% of Clarity Report respondents. This challenge is particularly acute for small businesses, with 60% highlighting it as their number one concern. The transition to a new workforce must be managed carefully, as maintaining high quality standards is crucial.
A new challenge identified this year is managing legacy systems, which ranks third overall. The difficulties of securing these systems, high maintenance costs, and loss of domain knowledge as experienced employees retire are significant issues. Legacy systems also hinder the incorporation of automation, a clear priority for manufacturers. Automation is increasingly seen as a solution to talent and quality control challenges, with 44% of respondents selecting it as a strategy for the upcoming year, rising to 60% among small businesses, which have a large gap to fill (only 14% automated versus 49% overall).
Implementing automation is complex, particularly for small and mid-size businesses that struggle with technology acceptance and the significant cost investments required. In contrast, the largest manufacturers cite scalability as their main challenge in building on their more advanced automated processes. Beyond automation, AI and machine learning (ML) are also key technological focuses. Implementation of AI/ML systems was the top digital transformation initiative, selected by 41% of respondents, up from 29% last year. Deploying more robotic automation tied for second among digital transformation initiatives at 36%, alongside process reengineering, a perennial focus for optimizing manufacturing and other business functions.
High-performing manufacturers, defined by the highest profit/loss margins, are leading the way in automation. Nearly all of this group (89%) report having automated operations, compared to less than half of the other respondents (43%). High performers view automation as a solution to talent challenges, with only 22% citing talent attraction and retention as a top challenge, compared to 35% of other respondents. Additionally, 56% of high performers leverage automation to address their challenges, versus 42% of the broader group. Their key performance indicators (KPIs) also differ, with only 11% tracking capacity utilization, the top KPI overall, while more than half of high performers (56%) track inventory turns.
Manufacturers are increasingly adopting technology to tackle talent shortages and quality challenges. The continuous turnover in the workforce has left manufacturers struggling to replace their most experienced workers. In response, automation, AI, and other technological strategies are becoming central. However, these innovations also bring unique challenges that manufacturers must navigate.
How does Costpoint™ help?
Streamlined Supply Chain Management: Costpoint™ enables aerospace and defense contractors to effectively manage complex supply chains by integrating procurement, inventory, and logistics processes. This integration ensures real-time visibility and coordination across the entire supply chain, reducing delays and improving efficiency.
Advanced Inventory Control: Costpoint™ provides robust inventory management capabilities that are critical for aerospace and defense contractors. It helps track inventory levels, manage stock locations, and monitor usage rates, ensuring that critical components are available when needed while minimizing excess inventory costs.
Automation with TIP SFE: By leveraging the Technology Integration Platform (TIP) with Shop Floor Execution (SFE), Costpoint™ automates various manufacturing and supply chain processes. This automation reduces manual effort, minimizes errors, and accelerates production cycles, leading to increased productivity and cost savings.
Enhanced Supplier Collaboration: Costpoint™ facilitates better collaboration with suppliers through its supplier management features. It allows contractors to manage supplier relationships, evaluate performance, and streamline communication, ensuring that suppliers meet quality standards and delivery schedules.
Real-time Analytics and Reporting: Costpoint™ offers real-time analytics and reporting tools that provide aerospace and defense contractors with critical insights into their supply chain operations. These tools enable contractors to make data-driven decisions, optimize supply chain performance, and quickly respond to changes in demand or supply chain disruptions.
Costpoint™ stands out as the only ERP developed specifically for government contractors, uniquely tailored to address the stringent requirements and complex challenges of this sector. Its comprehensive suite of tools ensures regulatory compliance, enhances project management, and provides accurate cost accounting, all while maintaining robust security and data protection. By offering advanced features for supply chain management and leveraging automation through platforms like TIP SFE, Costpoint™ empowers aerospace and defense contractors to optimize operations and achieve greater efficiency. Dedicated to the success and survival of the industry, Costpoint™ is an indispensable asset for government contractors, providing the specialized support necessary to thrive in a highly regulated and competitive environment.
Sep 25, 2024
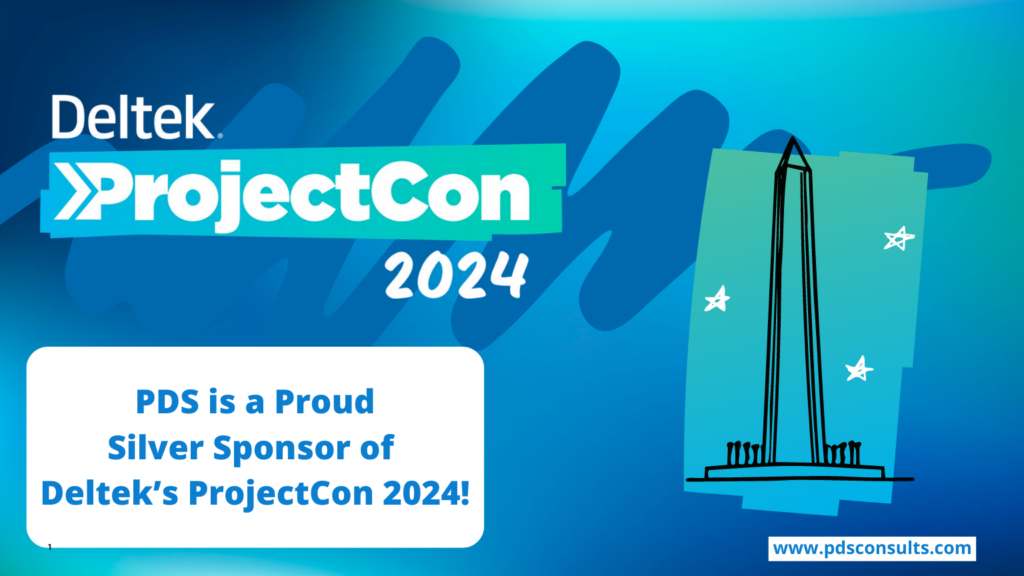
Join Us at Deltek ProjectCon 2024!
Deltek ProjectCon 2024 is the premier event for project-driven business professionals looking to elevate their skills, gain cutting-edge insights, and connect with industry leaders. From November 12-14 in National Harbor, MD, thousands of professionals will come together for three days of transformative learning, networking, and collaboration.
Whether you’re looking to optimize performance through expert-led breakout sessions or stay ahead with the latest innovations in Deltek Costpoint, this event has something for everyone. Sponsored by PDS Consulting Solutions, LLC, it’s an opportunity to connect with peers, explore new solutions, and drive success in your organization.
Date: November 12th – 14th, 2024
Location: Gaylord National Resort & Convention Center – National Harbor, MD
Swing By Our Booth: Kiosk 10A in the Expo Hall
Don’t miss out on this must-attend event for project-focused businesses. Register today and experience how Deltek ProjectCon 2024 can help you and your business thrive!
Jul 18, 2024
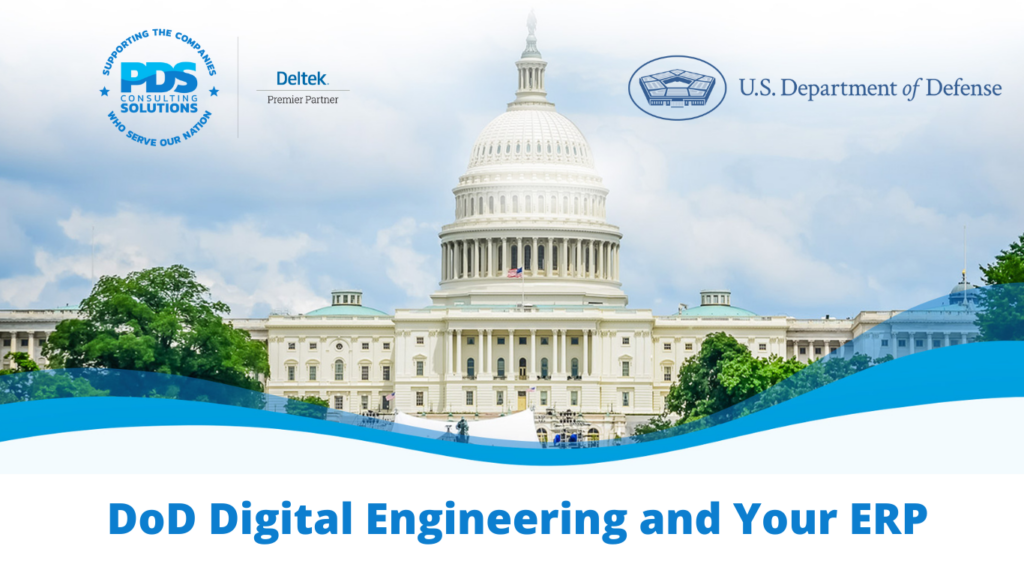
The Department of Defense Instruction (DoDI) 5000.97 establishes a comprehensive framework for integrating digital engineering methodologies, technologies, and practices throughout the lifecycle of defense acquisition programs. This directive, grounded in the authority of DoD Directive 5137.02, outlines policies, assigns responsibilities, and provides procedures to ensure the effective implementation and use of digital engineering in developing and sustaining defense systems.
Digital engineering involves the use and integration of digital models and relevant underlying data to support system development, testing, and sustainment. Digital engineering is critical for addressing global challenges, managing complexity, evolving technologies, and extending the longevity of systems. The benefits of digital engineering include enhanced decision-making, accelerated delivery of capabilities, and support for data-driven decisions. Digital engineering also offers considerable benefits for retaining skilled (and difficult to find) labor as well as providing for standard processes which allow for labor to be more efficiently utilized in a diverse manufacturing environment.
In acquisition strategies, digital engineering must be addressed comprehensively, detailing its usage throughout the system lifecycle and the expected benefits. Certain programs must include a digital engineering implementation plan in their systems engineering plan, as specified in DoDI 5000.88. Planning and financial resources are essential for implementing digital methods such as model-based systems engineering (MBSE), product lifecycle management, and computer-aided design (CAD).
New programs, pursuant to DoD directives, are required to incorporate digital engineering unless an exception is granted. The Under Secretary of Defense for Research and Engineering (USD(R&E)) is responsible for establishing policies, advancing practices, and developing workforce skills related to digital engineering. This role includes overseeing implementation in activities such as testing, engineering, software development, and system security, coordinating with DoD components, and leading efforts to define digital engineering data standards.
The Director of the DoD Test Resource Management Center (TRMC) is tasked with developing and maintaining DoD-wide digital engineering infrastructure, methodologies, and practices, and supporting distributed developmental testing capabilities. The Under Secretary of Defense for Acquisition and Sustainment oversees DoD intellectual property policy for digital engineering, leads adaptive acquisition framework pathways, and supports workforce training in digital engineering.
The Director of Operational Test and Evaluation develops practices for using digital engineering to meet testing objectives. The DoD Chief Information Officer (CIO) guides digital modernization and supports digital engineering for IT-based systems, providing risk management framework guidance. The Chief Digital and Artificial Intelligence Officer leads strategy and policy for data, analytics, and AI, facilitating data sharing and AI adoption. Heads of DoD Components with acquisition authority are responsible for implementing digital engineering procedures, supporting policy development, enhancing workforce competency, designating focal points for digital engineering activities, and guiding program incorporation of digital engineering practices.
The digital engineering capability must be accessible to all relevant DoD personnel and connect the phases of the acquisition lifecycle, supporting the development, verification, validation, and maintenance of digital models. This capability includes secure DevSecOps and test infrastructure, operating within a secure ecosystem using advanced data security methods and complying with privacy requirements. The digital engineering ecosystem comprises the necessary infrastructure and architecture to support automated approaches for system activities, including hardware, software, networks, tools, and workforce. Collaboration among stakeholders is crucial for developing models, simulations, and analyses.
Programs are encouraged to utilize existing DoD or Military Service-level digital engineering resources to the maximum extent possible before investing in new capabilities. The DoD TRMC provides core digital engineering infrastructure through initiatives like the Joint Mission Environment Test Capability and the National Cyber Range Complex (NCRC), which support various phases of the system lifecycle with high-fidelity, realistic cyber environments.
Maintaining digital models and authoritative data sources involves identifying and maintaining model-centric baselines, integrating technical data, and associated digital artifacts throughout the system lifecycle. Programs should use standard modeling representations, methods, and data structures to maximize interoperability. Digital models must be updated and maintained with real-world data, ensuring accuracy and utility for stakeholders. Verification, validation, and accreditation of digital models and simulations are required to ensure their reliability for decision-making and operational use.
How does generic ERP help you meet these new requirements for your digital engineering objectives?
Streamlined Data Integration: An ERP system should seamlessly integrate with digital engineering platforms, facilitating the smooth flow of data across various departments. This integration ensures that accurate and up-to-date information is accessible to engineers, enabling informed decision-making and efficient project management.
Enhanced Collaboration: By providing a centralized platform for communication and collaboration, an ERP system fosters teamwork among engineers, designers, and other stakeholders involved in digital engineering projects. Real-time access to project data, documents, and workflows promotes transparency and enables cross-functional collaboration, leading to faster problem-solving and innovation.
Agile Project Management: Ideally, your ERP solution offers robust project management capabilities tailored to the needs of digital engineering initiatives. From task allocation and scheduling to resource planning and budget tracking, the ERP system provides the tools needed to manage complex projects effectively. Agile methodologies can be seamlessly integrated, allowing teams to adapt to changing requirements and priorities swiftly.
Comprehensive Resource Planning: With features like resource allocation, capacity planning, and inventory management, your ERP system helps optimize resource utilization in digital engineering projects. Engineers can easily identify available resources, allocate them efficiently, and track their usage in real-time. This ensures that projects are adequately resourced, reducing delays and cost overruns. Resource Planning remains a pain point across industry and often requires an application outside of ERP.
Data Analytics for Continuous Improvement: Leveraging the wealth of data captured within the ERP system, the solution offers powerful analytics tools to support continuous improvement in digital engineering processes. By analyzing key performance indicators, trends, and metrics, engineers can identify areas for optimization, anticipate potential issues, and make data-driven decisions to enhance project outcomes and efficiency. The power of robust analytics, AI powered analysis and decision making is quickly becoming the new superpower of competitive advantage. While the R&D side of Aerospace & Defense manufacturing is truly cutting edge, many of the systems used to drive it remain disjointed, manual and brittle.
How does Deltek Costpointä provide more of what you need from your ERP to deliver the benefits of Digital Engineering to your customers and improve operational efficiencies?
Integrated Project Accounting: Costpoint seamlessly integrates project accounting capabilities with digital engineering workflows, allowing for accurate tracking of project costs, budgets, and revenue. This ensures financial transparency and compliance while providing insights into project profitability and resource utilization.
Lifecycle Management: Costpoint offers robust lifecycle management functionalities that support the entire digital engineering process, from conceptualization to design, development, and maintenance. Engineers can manage product configurations, revisions, and documentation within a single platform, streamlining collaboration and version control.
Resource Optimization: With advanced resource planning and scheduling features, Costpoint enables organizations to optimize resource allocation for digital engineering projects. Engineers can easily allocate personnel, equipment, and materials based on project requirements, availability, and skill sets, ensuring efficient resource utilization and project delivery.
Compliance and Risk Management: Costpoint incorporates comprehensive compliance and risk management capabilities tailored to the needs of digital engineering industries. From regulatory compliance to cybersecurity and intellectual property protection, the ERP systems help mitigate risks and ensure adherence to industry standards and regulations throughout the project lifecycle.
Analytics and Insights: Leveraging built-in analytics and reporting tools, Costpoint provides valuable insights into digital engineering performance metrics, project milestones, and key performance indicators (KPIs). Engineers can analyze project data in real-time, identify trends, and make data-driven decisions to optimize processes, improve project outcomes, and drive continuous improvement.
Digital Engineering is the new baseline for government contractors, and companies positioned to deliver against and exceed DoD expectations will gain considerable competitive advantage in the years to come. Costpoint is the only ERP built specifically for government contractors and is uniquely able to help you prepare for the new digital engineering future of the aerospace and defense manufacturing industry.
Aug 9, 2021
PDS is a proud Gigabyte Sponsor of our partner, Deltek’s, virtual 2021 conference. This global, project-focused, virtual event will deliver hundreds of live sessions, unique networking opportunities and of course, some fun – all accessible from anywhere!